Industry 4.0 requires a stable infrastructure
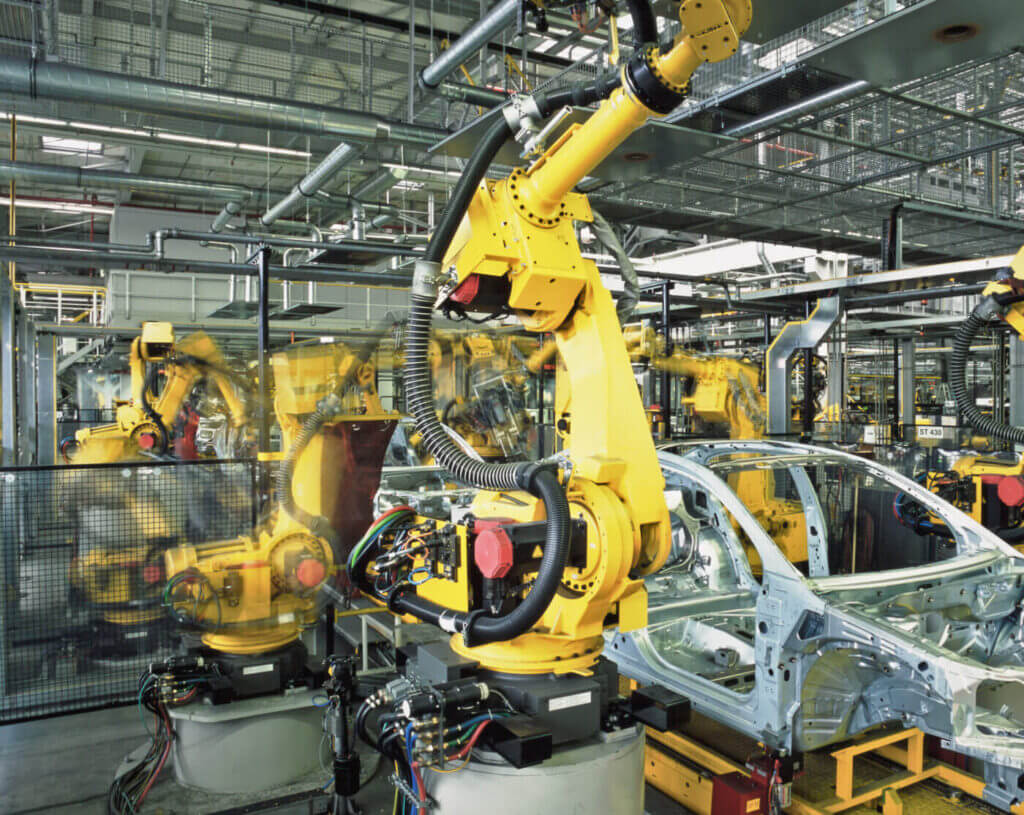
An uninterruptible power supply has always been essential for many industrial applications. With the increasing acceptance of Industry 4.0 concepts, the need for a reliable power supply for all aspects of production will continue to grow. It is important that the UPS masters its standard task but also copes with the specific requirements of an industrial environment.
Security is important in both traditional IT and production environments, but the focus is on different aspects. While IT environments largely balance their measures between confidentiality, integrity and availability, availability is the highest priority in production. Virtually all measures are aimed solely at ensuring that the production facilities function continuously. Until now, the power supply was primarily ensured at the elements that came into direct contact with the workpiece, such as the sensors of a CNC milling machine. This made it possible to obtain position data of the workpiece and milling heads and information on the milling head used in the event of a failure. This meant that production could continue almost seamlessly once the power supply was restored. If necessary, the entire system, including all actuators, was also supplied with emergency power in order to complete the entire production cycle.
Even more security required
Industry 4.0 will significantly increase the scope of protection in the near future. The Industry 4.0 mega-project networks components in production environments and provides them with their own intelligence. From now on, many more devices involved in a production process will record and collect data about it and pass it on to a higher-level instance. However, this also means that this data must be protected and buffered in the event of a power failure.
In principle, this task is no different in industrial environments than in classic IT applications, such as in a server room or data center. However, industrially used UPS systems are exposed to completely different environmental conditions and, due to the considerably lower level of standardization in industry, must be much more flexibly adaptable to the different areas of application.
Basic functions of a UPS
The basic function - to provide a clean output voltage - is initially common to all UPS systems. How the UPS achieves this goal can be technically accomplished in various complex ways. In the past, uninterruptible power supplies were referred to as online or offline systems and were assigned to a whole range of hybrid concepts that were based on one of the two main methods. Since 2003, IEC standard 62040-3 has put an end to the confusion of terms. A code based on the pattern XXX-YY-123 provides detailed information about the type and characteristics of the UPS. Class VFI UPS systems are particularly common in the professional sector. This represents the highest requirement and demands that the output voltage remains independent of fluctuations in the input voltage and frequency. This corresponds roughly to what would previously have been referred to as a double conversion or online UPS. The need to use a VFI UPS in the industrial sector stems from several conditions. For example, the mains voltage is often contaminated with high interference voltages and the switching of large electrical loads such as contactors, pumps or motors causes load peaks and voltage dips. A UPS that does not generate the voltage at the output completely synthetically would pass on such impurities to the connected loads. The UPS itself is also exposed to these disturbances. Resistance to interference, both conducted and radiated, must therefore be significantly higher in an industrial environment than in a normal IT environment. In addition, the UPS must be able to react as quickly as possible to high starting currents or similar dynamic load situations. With frequency converters in particular, the load currents often deviate significantly from the sine curve. The UPS system must also be able to supply these deviating loads. This can be achieved by designing the inverters accordingly or by additionally installing current filters.
Observe the power factor of the load
The faster the UPS system reacts to overvoltages, the better. In general, UPS systems without an output-side transformer have the edge in terms of reaction speed. They do not have to overcome the inertia of the transformer's inductive load and can therefore regulate load changes with very little delay. The power factor is also important, or rather the reaction of the UPS to the power factor of the load. Depending on the leading or lagging power factor, UPS systems with an output transformer do not deliver the full specified power. With a lagging power factor of 0.8, often only 60% nominal power is available, the full output power is only available with a power factor of 1. Transformerless UPS systems are more tolerant in this respect and deliver the full rated load even with lagging power factors.
In an industrial environment, UPS systems must adapt to the spatial requirements and the demands of the load. While the actuators of a machine are normally operated with 230 V or 400 V three-phase current, the control systems often run with 24 V direct current. Special UPSs are available for the 24 V supply, especially for use on a top-hat rail. They usually have external battery packs because the limited space does not allow for built-in energy storage. Depending on the user's concept, the power supply can also be fused before the low-voltage side, in which case the UPS is installed in a standard switch cabinet and supplies single-phase or three-phase mains voltage at the output. In such application scenarios, the UPS and its housing must also meet the mechanical requirements of the industrial environment. Protection class IP54 is often required to protect the electronics from splash water and dirt. If aggressive liquids are also used, an acid-resistant material such as stainless steel is required. And system integrators also require the appearance and design of the housing to be adapted to their own products.
Temperature as a decisive factor
Even if switch cabinets are often ventilated, the temperatures in them are different from the 20 °C normally found in IT. This has far-reaching consequences for the electronics of the UPS system and especially for the battery packs. While the UPS itself can be equipped for extreme temperatures by using higher-specification components, standard batteries are unsuitable for this. The guaranteed service life is normally specified at a standard temperature of 20 °C, deviations above this drastically shorten the time until replacement. It is therefore important that the UPS manufacturer can also use other energy storage devices. For example, batteries with an extended temperature range (e.g. Cyclone cells) are available, which have a three times longer service life of up to 15 years and a high tolerance to temperature fluctuations between -30 °C and +65 °C.
Such Cyclon cells are significantly more expensive than standard lead-acid batteries, but offer advantages particularly in environments where downtimes for maintenance must be reduced to an absolute minimum. Due to their low internal resistance, they are also able to deliver very high currents quickly, perfect conditions when a UPS has to absorb short-term load peaks.
Special feature: Regenerative power supply
One of the special features of an industrial environment is that the load can act like a generator from one moment to the next. If processes are to be completed in a controlled manner in the event of a power failure, for example to separate the tool and workpiece from each other in a defined manner, energy can flow back. Reverse energy is generated when the machine brakes and motors switch to generator mode. This energy flows back into the power circuit and counteracts the function of the UPS. If the energy is too high and flows over a long period of time, there is even a risk of a defect in the inverter and in the rectifier intermediate circuit. For this reason, UPS systems whose load could potentially feed back current must have special regenerative units. Normally, if this case is rare, the energy is simply converted into heat. If energy is frequently fed back, there are also systems that can feed the electricity into the public grid.
An industrial environment not only places special demands on a UPS system in terms of hardware. There are also different protocols and media for the communication of the system with the administrator and with the devices to be protected. An Ethernet port is usually provided as standard for communication, but a normal network does not cope well with the industrial environment, which is subject to electrical interference pulses. Industrial Ethernet or Profibus are widely used as alternatives for networking production systems. Ideally, the UPS can also operate such deviating connectors, media and protocols via plug-in modules. The previously common RS-232 interface is also susceptible to interference signals, so that USB or, even more securely, RS-485 is used for serial communication. System manufacturers often also require potential-free switching contacts to display the most important status messages of the UPS system via a warning light or to trigger further actions.
The bottom line: perfectly customized standard solutions are ideal
Industrial environments are anything but perfect for UPS systems. Physical factors such as dirt, temperature, humidity and vibrations must be warded off by an appropriately robust and durable system design. For example, the UPS should be able to use alternative energy storage systems with extended temperature ranges and high power density. Harmful electrical parameters such as coupled interference voltages, load peaks and regenerated energy also make life difficult for the guarantors of a continuous power supply. A standard UPS, which can also be used in data centers, is out of place in such an environment. Highly individualized special constructions are also not sensible for cost reasons. It is important that the manufacturer understands the requirements of the environment precisely and can adapt its UPS system perfectly to the customer's requirements without major modifications. This results in a cost-efficient yet technically sound UPS system for industrial use.